The Duty of Fasteners and Machining in High-Quality Product Layout
The Duty of Fasteners and Machining in High-Quality Product Layout
Blog Article
Navigating the World of Fasteners and Machining: Approaches for Accuracy and Speed
In the elaborate world of bolts and machining, the quest for accuracy and rate is a continuous difficulty that requires careful interest to information and tactical planning. From understanding the varied range of bolt types to picking ideal products that can withstand extensive needs, each step in the process plays an essential function in achieving the wanted result.
Understanding Fastener Types
When picking fasteners for a task, recognizing the different kinds readily available is important for making sure optimal efficiency and dependability. Fasteners come in a large range of kinds, each developed for particular applications and needs. Bolts are used with nuts to hold materials with each other, while screws are versatile fasteners that can be made use of with or without a nut, depending upon the application. Nuts, on the various other hand, are internally threaded bolts that friend with screws or screws, giving a safe hold. Washers are vital for dispersing the load of the bolt and avoiding damages to the material being fastened. Additionally, rivets are irreversible bolts that are excellent for applications where disassembly is not required. Recognizing the distinctions in between these bolt types is essential for picking the right one for the job, ensuring that the connection is strong, long lasting, and dependable. By choosing the proper fastener type, you can maximize the efficiency and durability of your job - Fasteners and Machining.
Picking the Right Materials
Understanding the relevance of picking the ideal materials is extremely important in making certain the optimum efficiency and dependability of the chosen bolt types discussed formerly. When it involves bolts and machining applications, the material option plays a critical role in figuring out the total stamina, resilience, rust resistance, and compatibility with the intended environment. Various products supply varying buildings that can significantly affect the efficiency of the bolts.
Usual materials made use of for bolts consist of steel, stainless steel, light weight aluminum, brass, and titanium, each having its distinct staminas and weak points. Steel is renowned for its high strength and longevity, making it appropriate for a large range of applications. Stainless steel supplies superb rust resistance, perfect for settings vulnerable to moisture and chemicals. Light weight aluminum is corrosion-resistant and lightweight, making it suitable for applications where weight reduction is critical. Brass is usually chosen for its aesthetic charm and excellent conductivity. Titanium is known for its exceptional strength-to-weight ratio, making it perfect for high-performance applications. Picking the best material involves thinking about elements such as stamina demands, environmental problems, and budget restrictions to make sure the desired performance and longevity of the fasteners.
Precision Machining Techniques

In enhancement to CNC machining, various other precision strategies like grinding, turning, milling, and boring play crucial roles in bolt production. Grinding aids attain great surface area coatings and limited dimensional resistances, while transforming is commonly used to create round parts with accurate sizes. Milling and boring procedures are necessary for shaping and developing openings in fasteners, guaranteeing they satisfy precise requirements and description function appropriately.
Enhancing Rate and Performance
To enhance bolt manufacturing procedures, it is important to streamline operations and implement effective approaches that match accuracy machining methods. One key approach for improving speed and effectiveness is the execution of lean production principles. By reducing waste and concentrating on continual renovation, lean methods help remove bottlenecks and maximize operations. Additionally, investing in automation modern technologies can considerably boost manufacturing speed. Automated systems can manage repeated jobs with accuracy and speed, allowing workers to concentrate on even more complicated and value-added activities. Taking On Just-In-Time (JIT) stock management can additionally boost performance by guaranteeing that the right materials are offered at the correct time, lessening excess inventory and decreasing preparations. In addition, promoting a culture of cooperation and interaction amongst staff member can enhance general effectiveness by promoting transparency, problem-solving, and technology. By incorporating these strategies, manufacturers can achieve a balance between rate and precision, eventually improving their one-upmanship in the fastener sector.
Top Quality Control Actions
Executing strenuous quality assurance steps is critical in guaranteeing the integrity and uniformity of bolt items in the production procedure. Quality assurance procedures encompass various phases, beginning with the choice of raw materials to the final examination of the completed bolts. One fundamental facet of high quality control is these details carrying out thorough material inspections to validate compliance with requirements. This entails analyzing aspects such as material toughness, structure, and stamina to assure that the fasteners fulfill market standards. In addition, monitoring the machining refines is vital to promote dimensional precision and surface area coating top quality. Using sophisticated technology, such as automatic inspection systems and accuracy measuring devices, can enhance the accuracy and performance of quality assurance treatments.
Regular calibration of devices and machinery is necessary to keep uniformity in manufacturing and ensure that fasteners fulfill the necessary tolerances. Implementing stringent methods for recognizing and resolving non-conformities or issues is vital in avoiding substandard items from getting in the marketplace. By establishing a thorough quality assurance structure, producers can promote the track record of their brand and deliver bolts that satisfy the highest possible criteria of efficiency and durability.
Verdict
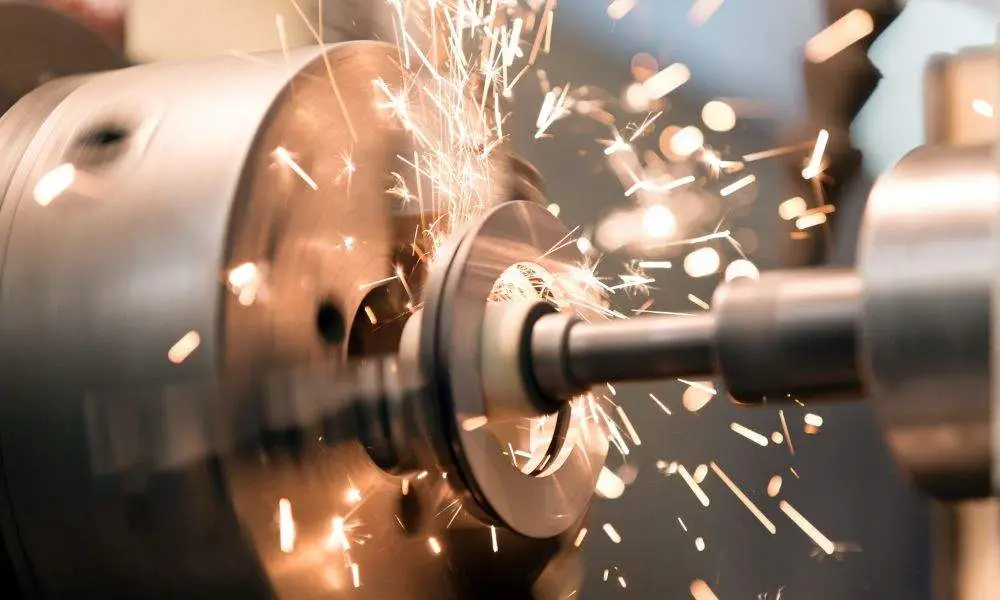
In the elaborate realm of fasteners and machining, the mission for accuracy and rate is a continuous obstacle that requires meticulous interest to detail and strategic preparation. When it comes to fasteners and machining applications, the material option plays a crucial duty in figuring out the general toughness, durability, deterioration resistance, and compatibility with the intended environment. Accuracy machining entails numerous sophisticated methods that guarantee the tight resistances and specifications required for fasteners.In enhancement to CNC machining, various other precision methods like grinding, transforming, milling, and drilling play essential duties in fastener manufacturing.To enhance fastener manufacturing processes, it is vital to streamline procedures blog here and implement effective strategies that match accuracy machining strategies.
Report this page